Project
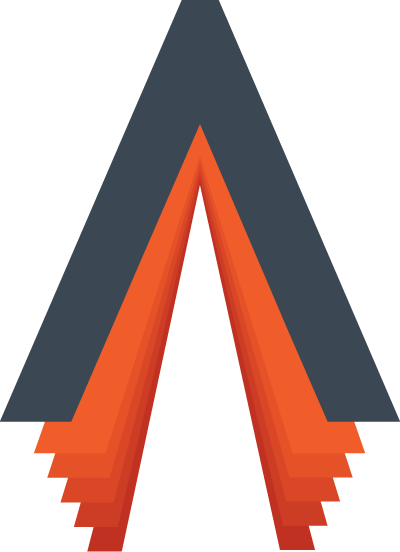
In order to mitigate the negative impact of human activity on the environment, significant efforts to lower carbon emissions are being pursued at both the global and European levels. Globally, the aviation industry aims for a 50% reduction of its carbon emissions by 2050, relative to 2005. In this transition towards net zero carbon emissions, novel powertrain technologies exploiting fuel cells and/or combustion systems that rely on hydrogen will play a significant role.
TRIATHLON will use the synergy between powertrain components to overcome the challenges associated with scaling up hydrogen powertrain technology to MW class. When the disruptive technologies developed by TRIATHLON are adopted by the industry, it will result in:
1) Reduction of emissions by implementation of NOx reduction strategies like injection of exhaust water of the FC into the CC and by capturing vented and permeated hydrogen and recompressing it;
2) Elimination of the need for a cryogenic pump by using a high-pressure storage buffer for pressurisation of the fuel distribution system (making the fuel distribution more robust for turbulence as well);
3) Reduction of the power required for hydrogen conditioning using excess heat from FC and CC by means of 3D printed heat exchangers using innovative materials like ceramics, and smart thermal management;
4) Improvement of the gravimetric index of the entire powertrain by providing an effective heatsink to powertrain components, reducing the need for coolant, allowing design of a more compact and lightweight CC, as well as the need for insulation of the hydrogen storage whilst enabling a longer dormancy time.
Acronym: TRIATHLON |
Full title: Thermodynamics-driven control management of Hydrogen powered and electrified propulsion for aviation |
Grant Agreement no: 101138960 |
Start Date: 01/01/2024 |
End Date: 31/12/2027 |
Duration in months: 48 |
Project budget: € 3 998 865.00 |
Funding scheme: Research and Innovation Action (RIA) |
Funding programme: Horizon Europe |
Call identifier: HORIZON-CL5-2023-D5-01 |
Keywords: Hydrogen, Thermodynamics, Multidisciplinary research, sustainable transport |
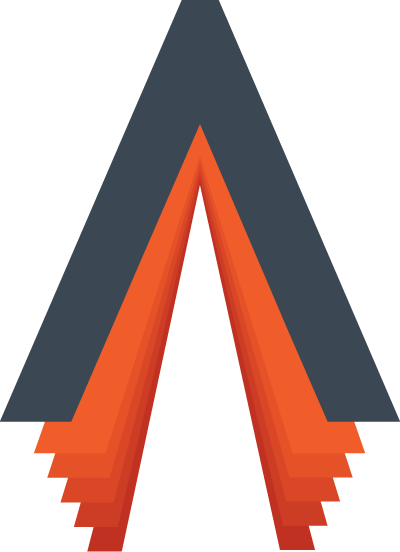
The project work is divided into 6 Work Packages (WPs). All of them will start in M1 and finish in M48.
WP1 Hydrogen Conditioning Requirements (TU Delft)
WP2 Thermodynamics Controlled Storage (TU Dresden)
WP3 Thermal management and thermodynamic performance (Sabanci Univeristy)
WP4 System-level analysis and technology roadmap (ERGON)
WP5 Dissemination, Communication & Exploitation (AMIRES)
WP6 Project management (M2i)
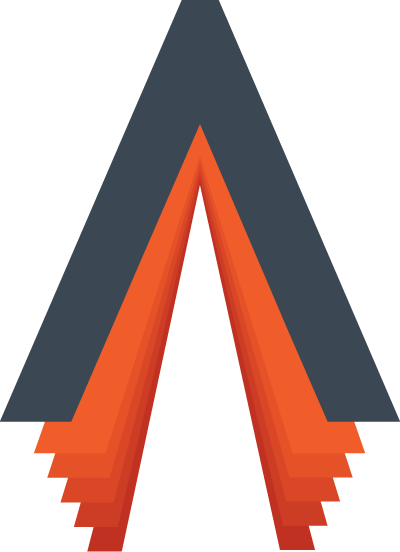
The ambition of TRIATHLON is the development of disruptive approaches to design more robust, low-maintenance, low-emission, highly responsive hydrogen-electric powertrains for megawatt class aircraft. This goal will be achieved by consistently pursuing the following objectives:
- Develop and investigate the feasibility of target-oriented storage solutions for higher gravimetric density and lower loss to atmosphere, increasing safety and reducing cost.
- Develop a hybrid power generation system that achieves high efficiency, power density, and ultra-low NOx emissions.
- Characterize interfacial heat and mass transfer of hydrogen phase change flow and define thermal management (TM) solutions based on structured mini-channels.
- Assess these technologies and draw a roadmap to further increase the TRL.
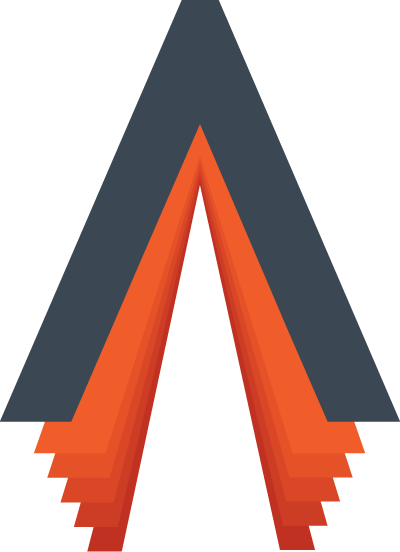
The TRIATHLON project aims to achieve significant outcomes in developing enabling technologies for a hydrogen-electrified megawatt-scale powertrain to achieve a TRL3, thus enabling the further development of the technology to higher TRL in time for its deployment on next generation aircraft by 2035-2050.
For the aviation and space industry, the expected outcomes include:
- FC thermal management is improved to reduce the coolant flow rate.
- Instabilities and emissions associated to hydrogen combustion are controlled with fuel temperature and water injection.
- Concept design of a multi-state storage system requiring no cryopump and with no H2 boil-off to the environment.
- Lab testing of thermal management coupons by 3D printed technical ceramic materials.
- Design of thermal management components using innovative tools based on dynamic simulation of the whole fuel system and its components to assess control approaches and to regulate the powertrain during the flight envelope.
- High-fidelity reactive simulations will provide clear directions to set up scaled-up, follow-up experiments with H2 combustion and water injection at TUD.
- Higher gravimetric/volumetric energy density of all-composite CcH2 storage systems without metallic liners (up to 80g/l for CcH2 vs. 40-60 g/l for GH2 or LH2).
- Lower cost of the H2 fuel system due to the absence of the cryopump (about 100k€ saved).
- Reduction in weight of the thermal management system due to lower coolant flow rate and more compact heat exchangers (at least –20% weight versus traditional manufacturing techniques).
- Quantification of the energy book-keeping of the fuel delivery system (parasitic energy losses).
All industries benefiting from CcH2 storage, the expected outcomes include:
- Sophisticated test methods for measurement of damage-dependent leakages, permeability, and heat transfer for composite and polymeric materials with cryo-compressed hydrogen.
- Identification, characterization and determination of damage in fiber composites by computational evaluation of CT-data.
- Testing the heat transfer performance of 3D printed technical ceramic material with different fluids, including CcH2.
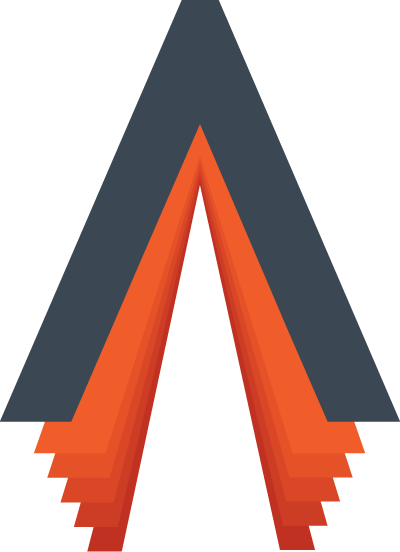
H2-EU-Project-Cluster
H2-EU-Project-Cluster is a small cluster of 4 projects, all focused-on hydrogen, whose main objective will be to establish synergies between the projects and to create the conditions to follow up on the current projects and take them to TRL5-6.
HYLENA: HYdrogen eLectrical Engine Novel Architecture. HYLENA will investigate, develop and optimize an innovative, highly efficient, hydrogen powered electrical aircraft propulsion concept. This is based on the integration and combination of Solid Oxide Fuel Cells (SOFC) with turbomachinery in order to use both the electric and thermal energy for maximisation of propulsive efficiency. This project will investigate a low level TRL concept and bring it to TRL3 in 42 months prior to a demonstrator in phase 2.
FlyECO: Future enabLing technologies for hYdrogen-powered Electrified aero engine for Clean aviation. FlyECO will develop a simulation and evaluation framework in which the optimal architecture definition of the Integrated Power and Propulsion Systems, the key enabling integration technologies and necessary controls concepts can be explored, investigated closely and advanced towards TRL3 through Proof-of-Concept (PoC) demonstrators. The project duration is 36 months.
ExFAN: Novel recuperation system to maximize exergy from anergy for fuel cell powered geared electric aircraft propulsion system. To achieve climate neutrality in aviation by 2050, hydrogen powered aircraft propulsion can be key. The ExFAN project will include a ducted heat exchanger in the nacelle of the propulsion system. It will use the ram jet effect to generate thrust from waste heat. The ExFAN system will be included in a geared electric fan propulsion system of mega-watt class powered by hydrogen fuel cell technology. The project duration is 48 months.
ClimAvTech
ClimAvTech is a cluster of 13 EU-funded projects working to mitigate the climate impact of aviation.
MINIMAL Project – Minimum environmental impact ultra-efficient cores for aircraft propulsion
BeCoM – Better Contrails Mitigation
MATISSE Project – Multifunctional structures with quasi solid-state Li-ion battery cells and sensors for the next generation climate neutral aircraft
OVERLEAF – nOVel low-prEssure cRyogenic Liquid hydrogEn storAge For aviation
EFACA – Environmentally Friendly Aviation for all Classes of Aircraft
HESTIA – HydrogEn combuSTion In Aero engines
HYLENA Project – HYdrogen eLectrical Engine Novel Architecture
FlyECO – Future enabLing technologies for hYdrogen-powered Electrified aero engine for Clean aviation
EXFAN – Novel recuperation system to maximize exergy from eanergy for fuel cell powered geared electric aircraft propulsion system
MYTHOS – Medium-range hybrid low-pollution flexi-fuel/hydrogen sustainable engine
FFLECS – Novel Fuel-Flexible ultra-Low Emissions Combustion systems for Sustainable aviation
HOPE Horizon Europe project – Hydrogen Optimized multi-fuel Propulsion system for clean and silEnt aircraft